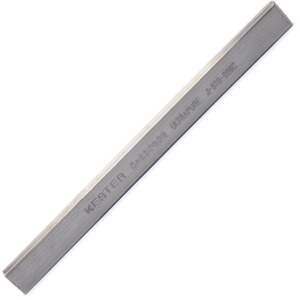
Qty: | Price: | Savings |
---|---|---|
1 | $53.18 | |
5 | $51.58 | Save |
10 | $50.52 | Save |
25 | $49.46 | Save |
100 | $49.03 | Save |
- Description
- Specifications
- Documents
Note: Due to a production delay, only cast bar will be available once current stock runs out. The cast bar alternative is CB44-6337-0050
Solder Bar, Leaded, Sn63Pb37, Zero-Halogen, 1-2/3lbs, Ultrapure
Tin-Lead (SnPb) Solder Bar
Kester Ultrapure Tin-Lead (SnPb) solder bars are designed for electronic soldering applications requiring high reliability, especially in surface mount assembly. Each batch is produced under tightly controlled conditions to reduce oxides and eliminate metallic and non-metallic impurities. The result is a solder alloy with excellent flow characteristics, low surface tension, and consistent performance.
Ultrapure solder conforms to IPC/J-STD-006C and meets the strictest quality control standards in the industry. When purchased directly or through authorized distributors, purity is certified for each lot.
Storage, Handling and Shelf Life
Store in a dry, non-corrosive environment between 10°C and 40°C (50°F–104°F). Over time, the surface may darken or appear dull, which does not affect performance. Shelf life is two years from the date of manufacture for alloys containing more than 70% lead, and three years for other compositions.
Extruded Bar # | Cast Bar # | Alloy | Lead Content | Halogen Content |
44-6337-0050 | CB44-6337-0050 | Sn63Pb37 | Leaded | Zero |
44-9574-0050 | CB44-9574-0050 | K100LD | Lead-Free | Zero |
44-6337-0030 | CB44-6337-0030 | Sn63Pb37 | Leaded | Zero |
44-7068-0000 | CB44-7068-0000 | Sn96.5Ag3Cu.5 | Lead-Free | Zero |
44-7050-0000 | CB44-7050-0000 | Sn96.3Ag3.7 | Lead-Free | Zero |
44-6040-0050 | CB44-6040-0050 | Sn60Pb40 | Leaded | Zero |
44-7080-0000 | CB44-7080-0000 | Sn95Sb5 | Lead-Free | Zero |
44-7000-0000 | CB44-7000-0000 | Sn99 | Lead-Free | Zero |
44-0595-0000 | CB44-0595-0000 | Sn5Pb95 | Leaded | Zero |
Extruded Bar vs. Cast Bar Process
Wave solder / Selective solder “make up bar” is available in multiple sizes and shapes: Cast, Extruded, Anode, Ingot, etc. Regardless of shape, the purpose of the bar is to replace material in the pot that is removed during the manufacturing process or with the dross. The key is that the bar alloy is always the same no matter the shape of the bar.
With “conventional bar”, the most common shape is either Extruded or Cast. Alpha has historically manufactured Cast Bar. Extruding is a more expensive way to produce bar solder when compared with cast bar.
Is there any difference between Extruded bar vs Cast bar regarding the alloy?
No. Once an alloy is manufactured and ready for forming, the shaping process, whether, extruded or cast, has no impact on the alloy. Extruded and Cast meet the same technical requirements and specifications as they are the exact same alloy and come out of the same master pots.
Is there a difference in the shape between Extruded bar vs Cast bar?
Yes. Specific to the shape and size, there are small differences. Extruded bar has a more consistent size and shape as it is pressed through a die
What is the Extruded Bar manufacturing process?
First the solder is made into the desired alloy, (SAC305, Sn63 etc.) in the master pot.
Second, as the alloy in the master pot is cleaned of excessive dross and made ready for forming.
Third, the solder is formed into billets to be used in the extruding process.
Finally, billets are placed into the forming equipment and forced or extruded through a die, resulting in the desired shape. Bar is then boxed for shipping.
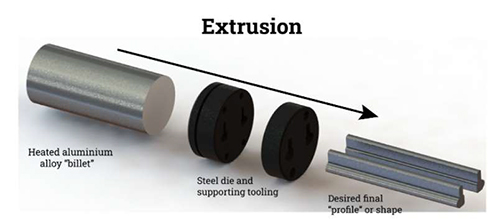
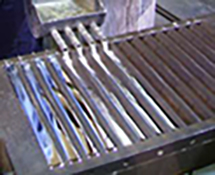
What is the Cast Bar manufacturing process?
First, the solder is made into the desired alloy, (SAC305, Sn63, etc.) in the master pot.
Second, as the alloy in the master pot is cleaned of excessive dross and made ready for forming.
Third, molten solder is poured directly into a mold or cast and then cooled. The solidified bar is then boxed for shipping.
Differences in using Extruded bar vs Cast bar?
Extruded bar is more expensive due to the extra steps required to make the extrusion. Cast bar is formed through a less expensive process.
Some equipment has bar solder auto feeders used to top off a wave solder pot which includes a die hole through which bar is fed into the pot. The Extruded Bar, being more consistent in size, may fit better though the die hole of the auto-feeder.
When bar solder is hand fed into the pot, cast bar is preferred, as there is no advantage in using the more expensive extruded processed bar.
Potential Limitation for Lead-Free Cast bar:
Some Electrovert wave soldering machines have a lead-free bar solder option that requires the use of a triangular shaped bar. Our triangular shaped extruded bar fits this equipment. This design is to prevent tin-lead solder from being added into a wave solder machine running lead-free.
This option is only on some Electrovert machines, and we have no knowledge of any other manufacturers with this requirement.
If you plan to convert a customer from extruded bar to cast bar it is advised to inquire if the equipment they use has any limitations on the dimensions of the solder bar.
Qty: | Price: | Savings |
---|---|---|
1 | $53.18 | |
5 | $51.58 | Save |
10 | $50.52 | Save |
25 | $49.46 | Save |
100 | $49.03 | Save |